光纤跳线降低插入损耗的方法介绍
发布时间:2020-03-19
1. 横向错位与插入损耗
造成光纤连接器插入损耗的主要因素有横向错位、端面间隙、直径失配和倾斜连接等,国内外公司和研究单位均对此展开过详细的实验和工程定量研究。如今,光纤连接器的光学性能和重复性也得到了明显改善,从初期 0.5-1 dB 的插入损耗下降到如今 0.2dB 的水平;插拔 500 次后,插入损耗变化量可控制在 0.1 dB 以内。
在光纤对接工程应用过程中,由于纤芯横向错位引起的损耗叫错位损耗,它是光纤连接中插入损耗的主要来源,特别是对于单模光纤。不考虑其他因素下,光纤横向错位导致的连接损耗可近似计算如下:

其中 d 表示两对接光纤错位距离,ω表示光斑分布函数。图 1 描述了典型单模光纤(光斑能量分布近似为高斯分布)纤芯横向错位与插入损耗之间的关系曲线:
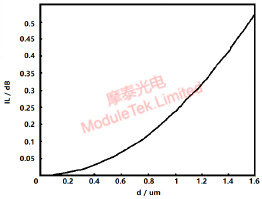
图1 单模光纤纤芯横向错位距离与插入损耗的关系曲线
光纤连接器纤芯的横向错位由多个因素决定,如陶瓷插芯的内孔与外径同心度,纤芯固化位置与插芯孔的同心度,多芯排列中的位置偏差等。目前加工工艺较好的插芯内孔同心度可达到 0.3 um 以内,而由于陶瓷插芯的内孔略大于光纤直径,所以在利用固化胶将光纤与陶瓷插芯固定时,光纤几乎不可能刚好位于正中心位置,也会带来一定的偏心量。插芯内孔直径一般比光纤直径大 0.5 um 以上,因此总体可产生 1-1.3 um 的同心度变化范围,即横向错位。从图 1 看出,对应大约 0.2 dB 的插入损耗,也即目前工业界中主流插损范围。若想使损入损耗小于 0.1dB,需将横向错位控制在 0.7 um 以内。
想要降低光纤连接损耗,首先要降低它的横向错位,工业上主要有两种方式:
①通过调点工艺,将所有纤芯偏心位置都调整到连接器固定区域。
②改善加工/组装工艺,提高纤芯同心度。
2.调点工艺降低插入损耗
调点工艺,是针对预组装的光纤连接头,通过把不同纤芯偏心位置都调整到一个区域内,实现偏心位置相互补偿,达到减小总体横向错位效果的方法。典型预组装陶瓷芯由陶瓷管和尾座组成(图 2、图3),尾座与套管之间存在凸凹插槽用于固定插芯。根据美国电子工业联盟 TIA/EIA 标准的建议,尾座上的四个插槽均匀分布在圆周上,通过旋转插芯可以使偏心量与指定位置(Key 键,也称定位键,见图 3、图 4示意点)之间的夹角控制在±22.5°以内,即两个连接头相连时,偏心量夹角在±45°以内。
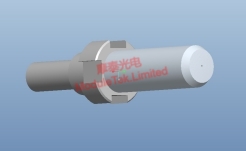
图2 典型插芯3D图
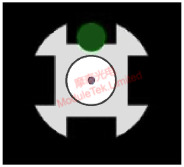
图3 典型插芯及 Key 键(绿色点对应位置)示意图
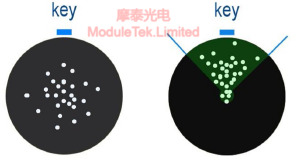
图4 偏心量调整后分布区域(上)及主要参数(下)
图 4示意了调点工艺处理后的插芯偏心位置区域,调点效果主要由区域夹角 H,最大区域半径 F,及中心区域半径 G 描述,表 4 列举了 IEC 61755 (2005)分类下不同等级插芯对应的参数值。显然,偏心区域越集中(H、F、G 值越小),插芯等级越高,代表纤芯同心度越好,连接时产生的横向错位越少,对应的插入损耗也越小。
表1 插芯等级与偏心区域参数关系(IEC 61755 (2005)标准)
Ref
|
Units
|
Grade A
|
Grade B
|
Grade C
|
Grade D
|
||||||||||||
PC
|
APC
|
PC
|
APC
|
PC
|
APC
|
PC
|
APC
|
||||||||||
Min
|
Max
|
Min
|
Max
|
Min
|
Max
|
Min
|
Max
|
Min
|
Max
|
Min
|
Max
|
Min
|
Max
|
Min
|
Max
|
||
F
|
\
|
0
|
0.6
|
0
|
0.6
|
0
|
1.2
|
0
|
1.0
|
0
|
1.5
|
0
|
1.4
|
0
|
1.6
|
0
|
1.5
|
G
|
\
|
0
|
0.1
|
0
|
0.1
|
0
|
0.3
|
0
|
0.2
|
0
|
0.3
|
0
|
0.3
|
NA
|
NA
|
NA
|
NA
|
H
|
\
|
0
|
50
|
0
|
50
|
0
|
50
|
0
|
50
|
0
|
50
|
0
|
50
|
NA
|
NA
|
NA
|
NA
|
调点工艺可由自动化同心度测试仪器完成,例如 Norland 公司 Centroc,Data-Pixel公司 Koncentrik,维度科技 Core Turner 系列产品。调点前后,插损可以明显改善并控制在一定的范围内(表 1):
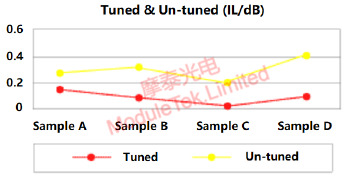
图5 调点前后插入损耗典型变化示意图
3.提高预组装插芯纤芯同心度
物理尺寸上提高预组装插芯纤芯同心度是降低横向错位的最根本的方法,但是由于受材料加工工艺、插芯制造工艺、穿纤定位控制工艺等的影响,想要通过此方法获得超越行业水平的产品,需利用超精密控制机械设备,费用成本较高,只有具备一定规模的企业会予以考虑。
3.1 陶瓷插芯制造工艺
目前陶瓷插芯制造工艺多样,典型方法为先使用氧化锆材料制作插芯毛胚,用注塑成型的方法形成 120 um 左右直径的内孔,然后进行内孔、外径精密加工。精密加工过程中,将插芯毛胚穿在一条粗细不一的特制钢丝上,通过旋转和移动插芯将内孔磨大,直至达到 125 um 或其他要求的数值。外径则通过旋转装置和砂轮反复磨削以提高同心度。目前,此工艺可以获得同心度在 1 um 以下的陶瓷插芯。
要提高插芯内孔、外径同心度,可以从两个方面入手。一是提高插芯毛胚制作精度,如利用内孔不直的偏移量反馈来修整模具结构,修正料道结构,使毛胚插芯内孔偏移量达到最小。有公司研究人员测试过修整模具后制作的毛胚插芯 Z 方向的孔径偏移量可控制在 20 um 以内。二是提高外径加工精度,如改进磨削设备中导轮机构,优化排屑槽,降低磨削热量和磨削温度对产品的影响。经过改良后的磨削设备可以控制插芯内孔外径整体同轴度在 0.6 um 以内。
3.2 纤芯装配工艺
该方法近几年才开始试验和应用,利用光学观测(放大成像、机器视觉等)的方法,在光纤与插芯组装固化过程中实时检测二者的同心度,并实时调整纤芯位置以达到尽可能高的同心度。例如,中国计量学院的研究人员提出了一种紧凑型的机器视觉系统(图5),配合特定的 LED 照明方案和边缘检测算法,可以快速检测插芯同心度,与标称参数偏差约 0.01um 水平。
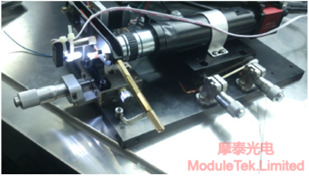
图6 光纤插芯同心度检测机器视觉系
  ; 虽然未规模应用,但该方法因照明和成像过程不需要接触物件端面功能区域,也不影响光纤组装过程,而且结果反馈速率快,可潜在应用于插芯与光纤装配过程中实时监测,并依次调整纤芯在插芯中的位置,优化预组装光纤插芯产品同心度。此方法可用于制造超高同心度的光纤连接产品,比如,0.3 um 及以下,逼近工业极限水平。
摩泰光电提供上述应用指南中涉及的商品,欢迎大家选购。